Machine Learning for Applications in Manufacturing
While modern manufacturing technology is starting to incorporate machine learning throughout the production process, predictive algorithms are being used to plan machine maintenance adaptively rather than on a fixed schedule. And these are only the tip of the iceberg.
Machine learning models can enhance nearly every aspect of a business, from marketing to sales to maintenance. In manufacturing, the rise of IoT, and the unprecedented amounts of data it throws off, has ushered in numerous opportunities to utilize machine learning. The computerization of industrial machinery is also undergoing rapid computerization. IDC data indicates that spending on IoT platforms will rise from $745 billion annually in 2019 to over $1 trillion in 2022.
According to a Global Market Insights report, global machine learning in manufacturing is going to skyrocket from $1 billion in 2018 to $16 billion by 2025. Alongside this, there will be a continuous need to reduce costs and grow the adoption of industry 4.0 technologies, including the predictive maintenance and machine inspection done by AI.
Examples of ML-based predictive maintenance
Machine learning enables predictive monitoring, with machine learning algorithms forecasting equipment breakdowns before they occur and scheduling timely maintenance. With the work it did on predictive maintenance in medical devices, deepsense.ai reduced downtime by 15%.
But it isn’t just in straightforward failure prediction where Machine learning supports maintenance. In another recent application, our team delivered a system that automates industrial documentation digitization, effectively reducing workflow time by up to 90%.
An automotive plant implemented a predictive maintenance solution for a hydraulic press used in vehicle panel production. Detailed studies of the maintenance process showed that engineers were spending far too much time attending to breakdowns instead of allocating resources for planned maintenance. The new solution enabled them to predict equipment failure with an accuracy of 92%, plan maintenance more effectively and offer greater asset reliability and product quality. Overall equipment efficiency increased from 65% (the industry average) to 85%.
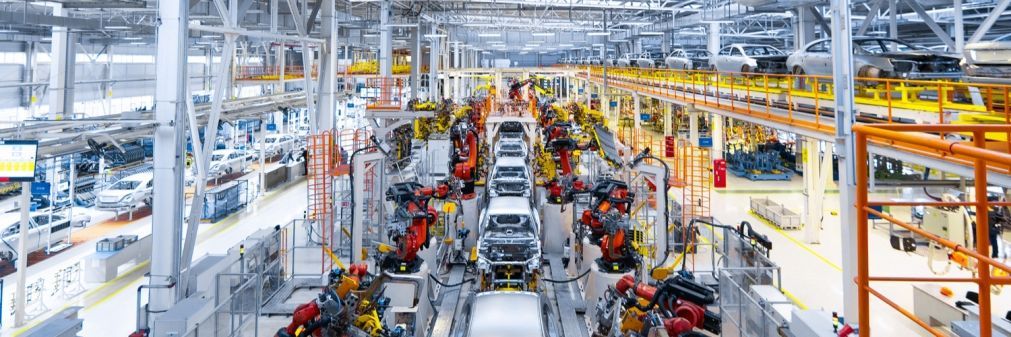
An automotive plant implemented a predictive maintenance solution for a hydraulic press used in vehicle panel production.
A beverage industry manufacturer of industrial equipment fit their machines with a monitoring and prediction system to help engineers plan better preventative maintenance. This solved the problem of inefficient, reactive customer service and helped to optimize equipment maintenance schedules, which had always been based on defined time intervals, rather than real needs. The application of machine learning increased business scalability and optimized the company’s cost structure.
Predictive maintenance is also expected to become an important technological component of autonomous vehicles. Self-driving cars are likely to follow the -as-a-service business model (rather than the ownership model of today’s car industry). That means cars will have to monitor their own condition rather than rely on their owner-driver to spot problems and take the vehicle to a service station.
Quality control
Artificial intelligence (AI) is also being adopted for product inspection and quality control. ML-based computer vision algorithms can learn from a set of samples to distinguish the “good” from the flawed. In particular, semi-supervised anomaly detection algorithms only require “good” samples in their training set, making a library of possible defects unnecessary. Alternatively, a solution can be developed that compares samples to typical cases of defects.
The savings machine learning offers in visual quality control in manufacturing vary by niche. In semiconductor manufacturing, the cost of testing and failures account for up to 30% of overall product costs. According to Forbes, automated quality testing done with machine learning can increase detection rates by up to 90%.
A manufacturer of agricultural product packing equipment has recently introduced a high-performance fruit sorting machine that uses computer vision and machine learning to classify skin defects. The operator can teach the sorting platform to distinguish between different types of defects and sort the fruit into sophisticated pack grades. The solution combines hardware, software and operational optimization to reduce the complexity of the sorting process.
Logistics and inventory management
It isn’t only on the assembly line and production plant where large strides have been made. Industry also requires an astonishing amount of logistics to power the entire production process. Employing machine learning-based solutions to handle logistics-related issues boosts efficiency and slashes costs.
According to Material, Handling and Logistics Magazine, the average US business loses $171,340 per year due to repetitive, mundane and time-wasting tasks like searching for order numbers, processing papers and calculating the value of orders. In any manufacturing company, logistics and production-related paperwork sap thousands of man-hours annually.
Resource management is another strength of machine learning-based algorithms. To see just how strong it can be, look no further than the power-consumption optimization algorithm Google applied in its data center cooling systems to reduce its electric bills–by up to 40%. That it was done without any infrastructure modernization or modification – the big data flowing through the system itself was enough – makes the feat all the more impressive.
Rising interest in machine learning applications in the manufacturing industry
Manufacturing companies now sponsor competitions for data scientists to see how well their specific problems can be solved with machine learning. A recent one, hosted by Kaggle, the most popular global platform for data science contests, challenged competitors to predict which manufactured parts would fail quality control. The participants needed to base their predictions on thousands of measurements and tests that had been done earlier on each component along the assembly line.
The competition was sponsored by Bosch, which is striving to trace causes of manufacturing defects back to specific steps in the production process, as well as support waste reduction by rejecting faulty components at early stages. The results of the competition are expected to improve product quality and lower costs.
The near future – robotics-powered manufacturing
Modern manufacturing, despite being largely automated, is still heavily reliant on the human workforce. Machines perform tasks to perfection–when they are in a closed environment–but performing a precise job in a more changing environment requires a human specialist.
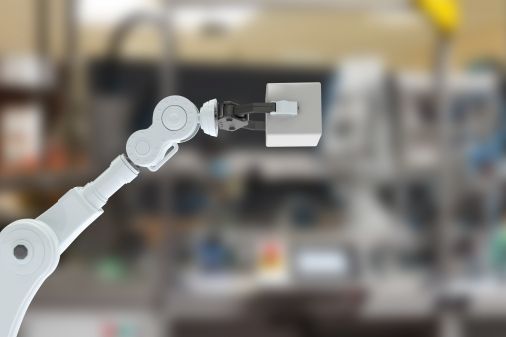
In the near future, a large part of manufacturing could be taken over by robots that are flexible enough to cooperate with humans
In the near future, a large part of manufacturing could be taken over by robots that are flexible enough to cooperate with humans and perform tasks in a more human way. They will be able to adapt to both the changing environment and the object being produced. Democratization and productization are among today’s leading AI trends.
Robotics provides a great opportunity for reinforcement learning. This machine learning technique is currently the only way for machines to adapt to a changing environment and build more complex strategies for achieving their goals, which are unachievable with explicitly programmed solutions.
deepsense.ai’s Research and Development Hub currently has several scientific projects supporting the application of AI in robotics, with expert augmented reinforcement learning and artificial imagination as a training environment.